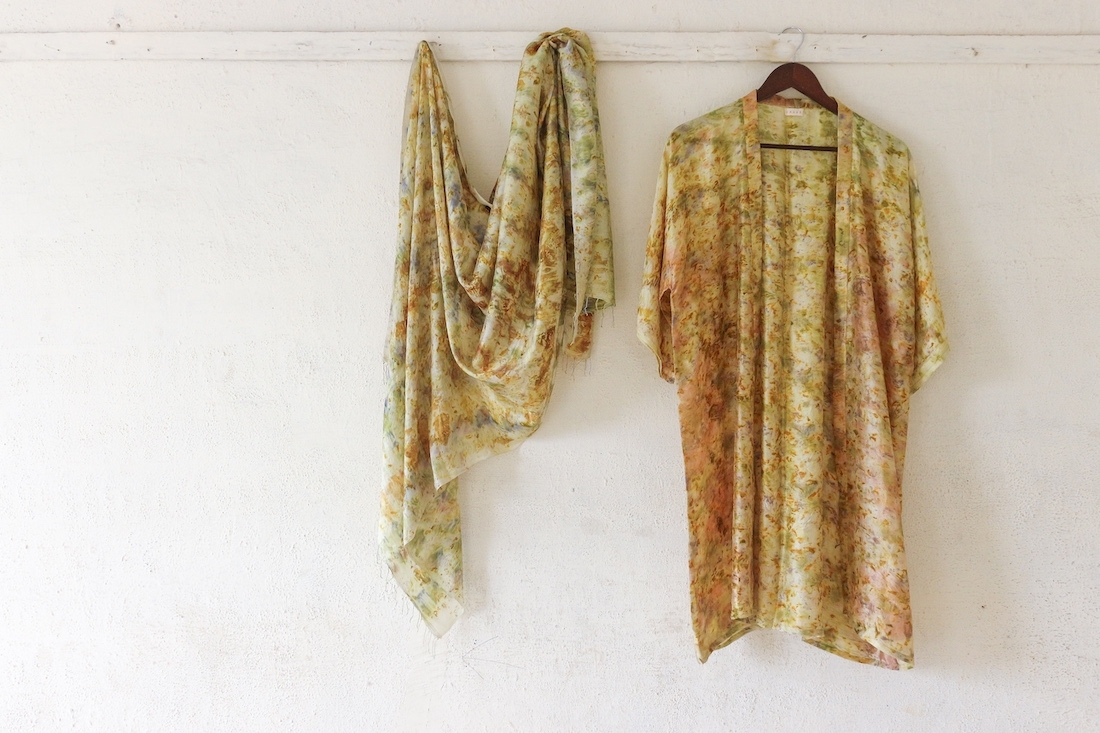
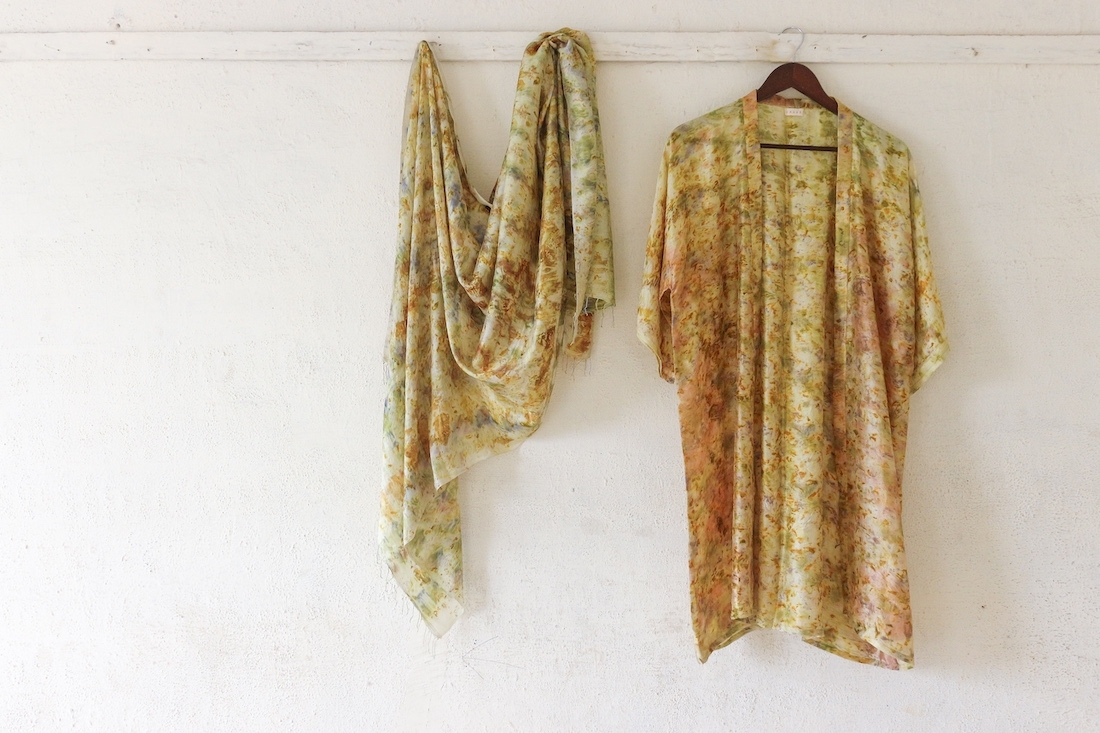
Florals for spring season may not be groundbreaking, cue Miranda Priestly’s deadpan expressions, but they’re a phenomena popular across the globe. What usually gets hidden within the silhouettes of the vivid hues and bright tones is the toxicity of synthetic dyes. Climate change is a harrowing crisis, yet many of us are rather clueless about the alarming truth of fast fashion and the extent to which our mindless consumption damages the ecology. Multiple reports by GreenPeace have established the release of excessive clothing dye, made up of chemicals, into water bodies close to textile factories in countries like India and China. While these not only pollute and deplete the country’s sources of freshwater, synthetic dyes are also carcinogenic and have the potential of eventually harming those wearing the clothes.
Sister duo Janhavi and Juhi Vyas, motivated by the documentary The True Cost, began exploring the process of natural dyeing and textile up-cycling, which eventually led to their label Akané. Both were creatively inclined since childhood and developed their fascination for textiles from their mother’s pan Indian saree collection. A postgraduate degree from the Srishti School of Art and Design led Janhavi towards the field officially, whereas Juhi’s degree in Fashion Communication from NIFT set her on the path.
Talking about the formation of the label Janhavi adds, ‘I collected un-dyed fabric trims, leftovers from fabric rolls, defective pieces of fabric, and anything I could get my hands on from the various garment factories. I dyed these with natural plant materials and designed a complete collection of naturally dyed and up-cycled garments. Post my graduation, I traveled around India to learn more about the process of natural dyeing from the fourth generation of artisans. A lot of exploration and experimentation led to me providing natural dyeing services to different brands, designers, and even an architecture firm. This is how Akané started off organically.’
The other half of the sister duo, Juhi came onboard a little later. She began by interning for fashion magazines, but couldn’t come to terms with the rampant consumerism and capitalism which pervades the very basis of the industry she always wanted to be a part of. She adds, ‘Then I started educating myself more about alternatives to fast fashion — slow living, sustainable fashion and an ethical supply chain. During this time my sister was already working with natural dyeing and Akané, and since I had always been interested in being an entrepreneur, it was the perfect opportunity for me. That’s when we started working on Akané as a brand and creating our own products.’
The sisters were drawn heavily towards the power of nature and the unhackneyed results it yields. Each time they are dyeing a product, they find themselves amazed at the ingenuity of the process — no two pieces are ever the same. Nature is unbridled, there are no set permutations and combinations they work with, the process is rather fluid. They further elucidate, ‘Natural plant materials have been used to dye fabric for a really long time. In India, the earliest evidence of natural dyeing is a piece of cotton dyed with Madder root (Manjishtha) which belonged to the Indus Valley Civilisation. So practicing this ancient technique is like going back to our roots, which we think is what slow living and a sustainable lifestyle is all about.’
The uncertainty of such a process comes with multiple challenges — they went through multiple failed experiments to deconstruct the process of natural dyeing. They like to take each day at a time and continue to learn more with each individual obstacle they face. Breaking it down further, they tell me, ‘We tend to think in the same way so we often have to almost force ourselves into thinking about being profitable and think of Akané as a business rather than just a creative outlet. Ideally, we would just love to give all our time to explorations, experiments, developing new techniques and products, but we also need to focus on generating profits and sustaining as a business. Being a slow fashion brand, selling naturally dyed and hand-dyed products means slower production which we don’t mind at all, but scaling up as a business can be a challenge when you’re the only two people taking care of everything.’
The entire discourse that surrounds natural dyeing posits it as a more wholesome option, a safer alternative to synthetic dyeing and rightly so, but the mammoth task isn’t easy to undertake. It all begins with preparing the fabric to be dyed, there’s two aspects to that — scouring and mordanting. The sisters, who do this all themselves, begin with washing the fabric with soapberries to get rid of any impurities, and fabric usually has a layer of starch on it, which they get rid of. This process is scouring. The next step is to mordant the fabric and the term mordant means something to bite into. So the mordant is crucial in helping the natural pigment seep into the fabric. What follows is a dye bath that is first soaked in the natural plant material overnight and heated to extract the colour, and this is just one of the techniques used.

Dyeing in process
This is just the tip of the iceberg, they further describe, ‘We source all our natural dye materials locally. Living in a city like Mumbai, there is so much waste produced around us, so we try to use as much of it as possible. We collect flower waste from temples and even local florists since so much of it is thrown out each day. We also collect flowers during festivals and religious occasions, dry them, and store it for use throughout the year. Some leaves are foraged locally, guava, and jamun leaves are collected from a farmer or from local vegetable vendors.’ In their line of work trash is good.
Janhavi and Juhi Vyas are working tirelessly with a holistic vision in mind. Their main aim is to contribute to a slower, more circular economy. With Akané they wish to create timeless products, garments that hold meaning — trends and seasons are futile. Steering clear from an industrial outlook, they invest in their clothes and goods with patience and dedication. The fabric is sourced locally from Indian artisans. Being directly connected to what they design, the sisters use and wear their initial samples to document how they feel and the kind of alterations required. They further, ‘interweave positive energy and intention into the piece of fabric while dyeing it, since it is such a meditative process.’
Like for many others, this massive global pause called Covid19 has put a halt to Akané’s operations as well. The sister duo isn’t letting that deter their will. They’re constantly ideating to be able to support the weavers involved in the business. Now more than ever, they are fuelled to help introduce more artisanal communities in the process of production. Instead of it just being the Vyas sisters at the forefront, they want to build a community more conscious of what it produces with the help of Akané. They wish to start programs equipping those in need with the skills for natural dyeing, hence aiding them to generate employment.
They had plans to teach workshops before the lockdown — they plan to sensitise younger, more impressionable minds to be more mindful about nature and the havoc humanity is wreaking on it. Apart from helping build a purposive space within the fashion industry, the two sisters are also keeping sane through embroidery and learning to hand weave on frame looms.
Text Unnati Saini