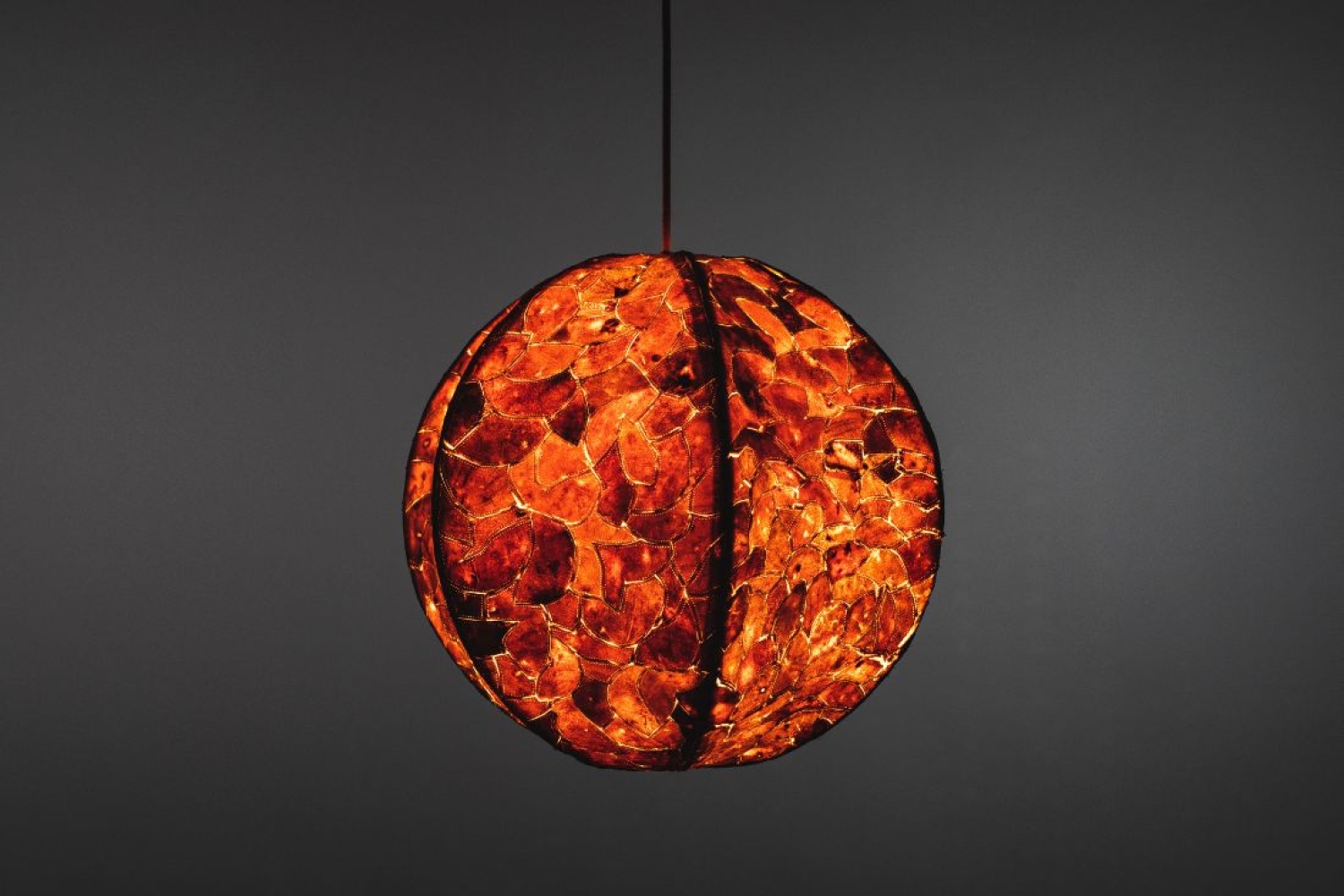
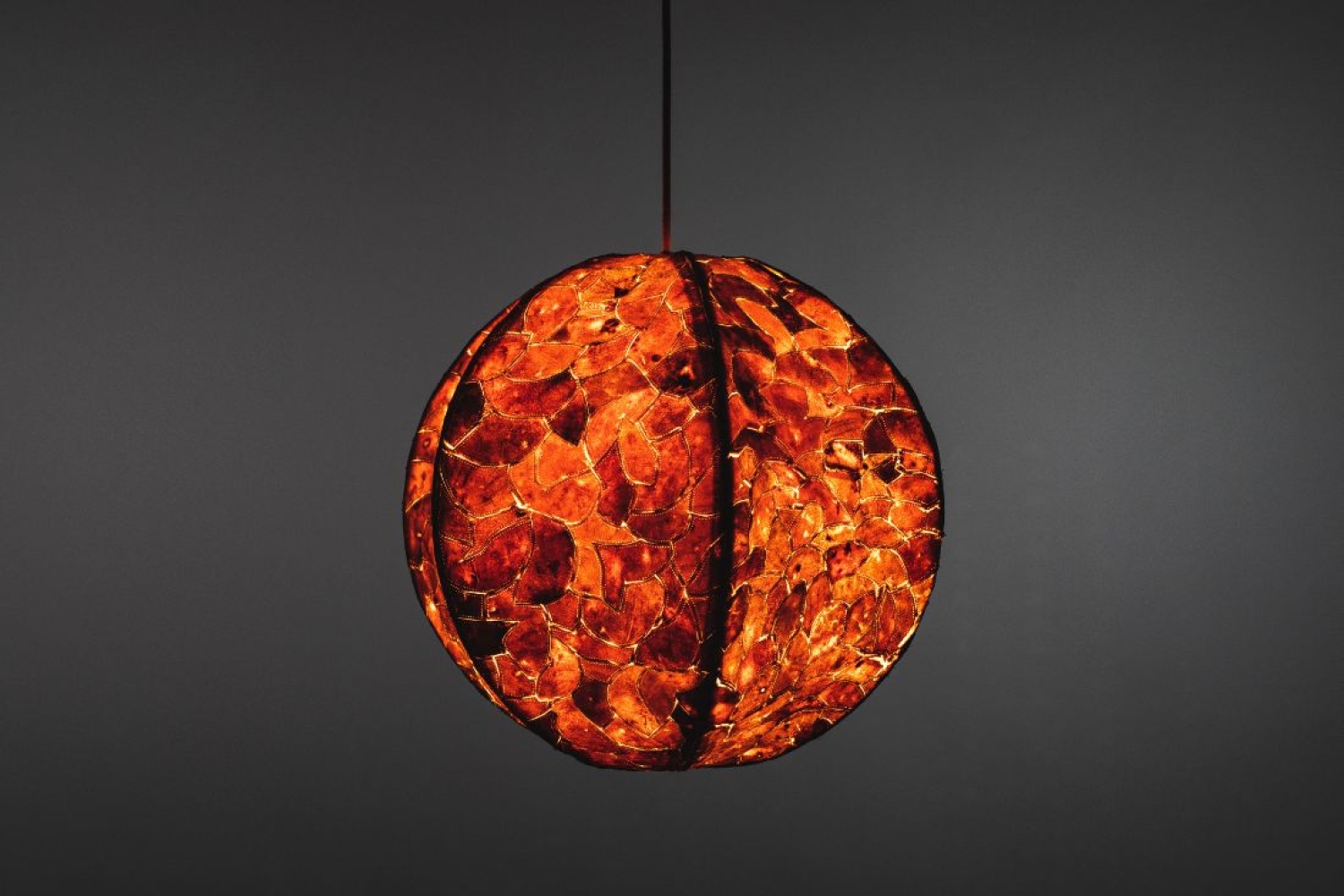
Alkesh Parmar, the innovative founder of Studio Arp, brings a unique perspective to sustainable design—one that is deeply rooted in his lineage as a member of the Mochi caste, who are known for their craftsmanship in shoemaking. With a lineage of skilled artisans behind him, Alkesh approaches design with a profound understanding of material culture and a commitment to repurposing waste. His work embodies a resourceful spirit, transforming discarded citrus peels into durable, leather-like materials that challenge conventional notions of waste and creativity.
In this interview, Alkesh shares how his background influences his design philosophy, his experimental journey with orange peels, and his dedication to non-Eurocentric perspectives in craft.
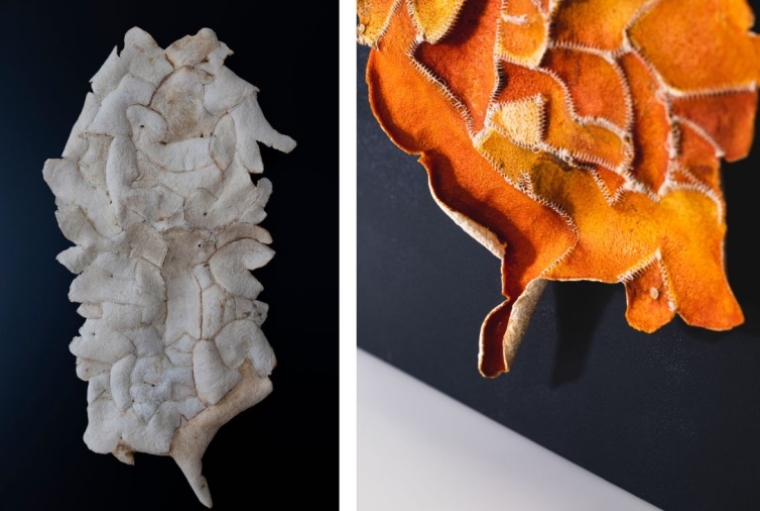
INFLUENCE OF LINEAGE
My heritage as a shoemaker stems from generations within the Hindu caste of Mochis, skilled in crafting and repurposing materials like leather into functional objects. This lineage has deeply informed my understanding of material culture and reinforced the importance of sustainable craftsmanship. My ancestors not only created and repaired shoes but also handbags, wallets, and other leather items, which fostered in me a natural inclination toward resourcefulness and reinvention. This background shapes my practice by encouraging a hands-on, low-tech approach, drawing from traditional skills to repair repurpose waste into innovative, sustainable materials. The relationship and connections with my lineage of leather shoemaking, repairing and the leather-like orange peel material was something that developed instinctively.
ORANGE PEEL
The idea came from a desire to explore local, natural waste materials and reimagine them in ways that would maximise their properties. Orange peel, often dismissed as waste, stood out due to its leather-like texture during certain drying phases, and its durability and preservation once dried. These qualities intrigued me, sparking exper- iments to harness the elasticity and durability of orange rind when nearly dry. I aimed to create a process that maximises natural resources and offers a biodegradable, sustainable alternative, transforming discarded peels into versatile new materials with potential in various art and design applications.
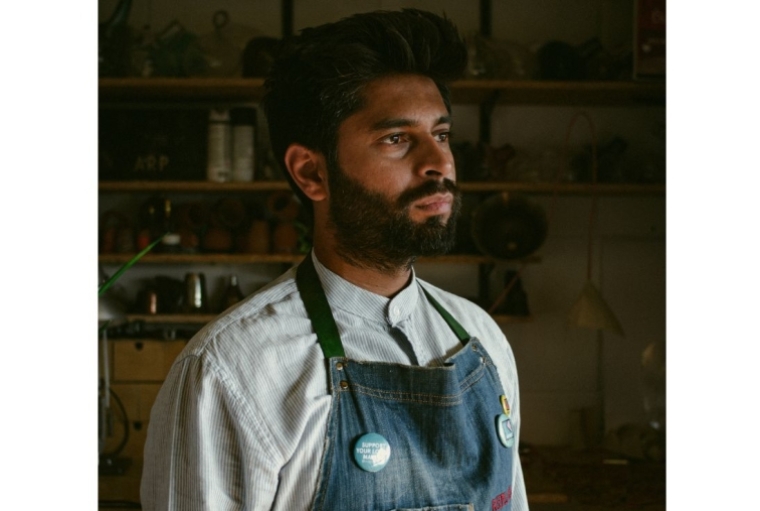
Alkesh Parmar
NON-EUROCENTRIC PERSPECTIVES
My background as a British-Indian maker made me acutely aware of the dominant Eurocentric narratives in design, which often overlook other cultural approaches and values in craft. By bringing my cultural heritage and the practical experience of my ancestors into the conversation, I aim to challenge and expand conventional perspectives in design. This includes a focus on decentralising design, utilising local materials, and examining how different cultures approach sustainability and material reuse, often in ways that differ from Western craft traditions.
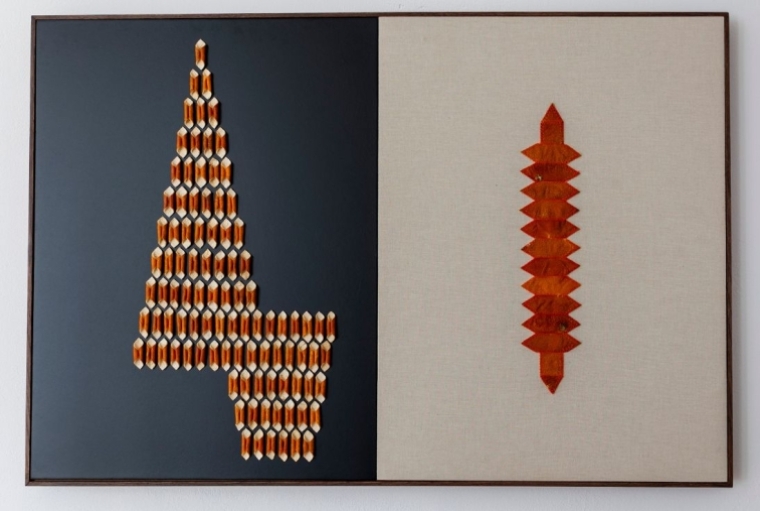
CREATIVE PROCESS
My process starts with researching the waste material itself—understanding its composition, structure, and unique properties. The material composition from waste orange peels includes pectin, cellulose, and soluble sugars derived from the peel, segment membranes, and seeds. These components are utilised in different ways to create various materials. The pectin is used as a binder with dried peel to create a composite. The cellulose in the waste is useful for making paper and card materials.
The leather-like material is composed of only orange peels which are sewn together with recycled thread. Developing the material involved extensive experimentation, particularly with drying times and environmental variables such as temperature and humidity, which affect the peel’s flexibility and mouldability. Discovering the optimal conditions of its leather-like quality required iterative testing to understand and control these factors. Initial iterations included wrapping peels around basic forms with tape and elastic band to understand how it behaved. The behaviour of the drying also depends on the variety of orange and how old it was before it was used for juicing, these variables impact the thickness of the pith (the white part of the peel). Once I understood these factors, I explored ways of creating larger materials, which led me to sewing them together, essentially patchwork. Each piece of orange is measured, cut to size, and sewn together piece by piece.
This process emphasises a low-tech, craft-oriented approach that encourages interaction and invites others to reconsider their relationship with everyday materials that minimise reliance on external resources, using local waste to create sustainable materials. It avoids synthetic additives, focusing instead on maximising the inherent properties of orange peel. Additionally, the prac- tice of dematerialising design—minimising material use and complexity—contributes to a sustainable, environmentally conscious approach.
Words Paridhi Badgotri
Date 14.11.2024